An asphalt batch plant produces asphalt in batch process. Each batch is of a mix material design which is made as per the requirement. But it is like any other big equipment which is transported in a dismantled condition. Like any piece of equipment we need to follow proper process and guideline for first time to start up and running. Due care has to be taken during the initial phase of the start-up of the machine to ensure longevity.
This post is about the first time to start up and points to note for an asphalt batch plant. It is notable to understand that it is highly recommended following these points to ensure minimum break down in case of long run of the machine. Make sure the machine is set to run, and all settings are done properly in the initial days of its operation. This will ensure that the breakdown chances are less in the long run.
An asphalt batch plant is also known as a tower type asphalt plant – Atlas is one of the leading manufacturer and exporter of the same. The key components like hot elevator, vibrating screen unit, hot bins and mixing unit are all in a single tower. Most of the operations of producing hot mix asphalt in batches is done in this tower unit. The tower is a big structure which is dismantled prior to transportation of the equipment.
All other components are containerized and modular and hence they require installation to be done on the job site in order to get the hot mix asphalt from the machine. Atlas does support its customers with technicians for on site support. This is support for supervisory erection and commissioning of the equipment.
Points to Note For First Time Start-Up Of Asphalt Batch Plant:
When the equipment arrives to the job site in a dismantled condition it becomes very important to install each component properly and take a dry trial run of them prior to the actual mix run. Below are some important points to note for the first time start-up of Atlas asphalt batch plant.
Atlas does support its customers with on site support for installation, operation and maintenance of the equipment. All the points are usually checked and taken care of by our technicians physically as they are present at the site. Due to COVID-19 we are unable to send our technicians to many job sites and hence this guide comes handy.
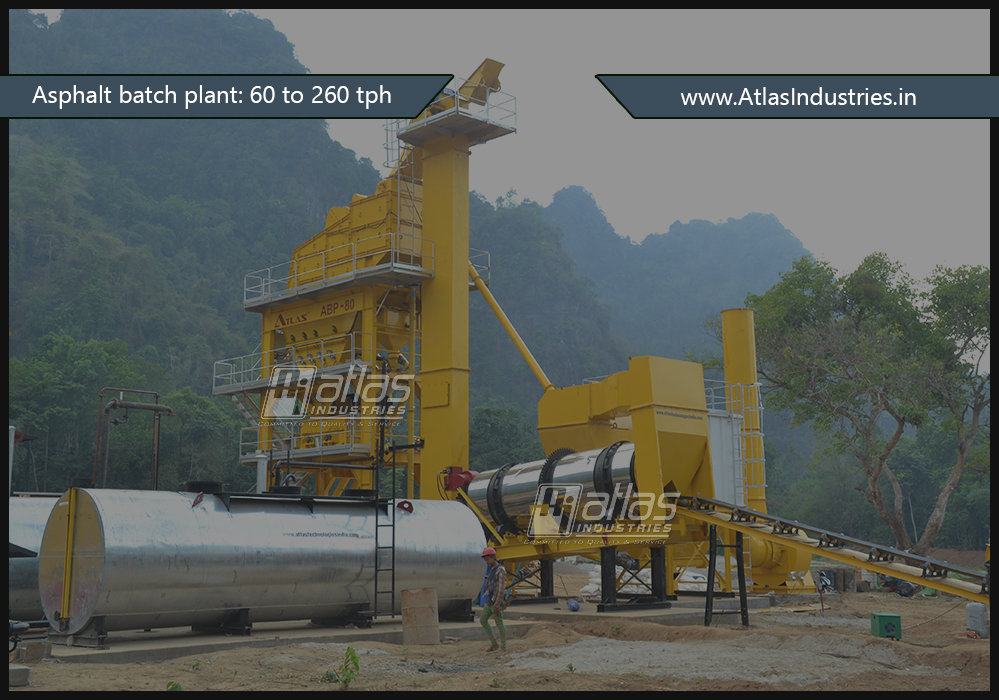
Things to Note Before Starting the Asphalt Batch Mix Plant
- All moving parts have to be greased before starting the plant.
- Oil to be filled in all the components before starting the plant.
- All feeder belts have to be set and aligned before starting the plant.
- After the first empty run, all nuts and bolts of the plant have to be tightened.
- The first 5-6 batches of plants operation have to dry batch. After that, tighten the vibrating screen nut bolts and mixer arms and tips and liner tighten and weld the same.
- Drum should rotate clockwise when viewed from the burner side.
- Opposite to the drum drive gear box there is an idler sprocket. Its shaft has to be daily greased.
- Dryer drum ring and sprocket has to be oiled and greased daily.
- Check the position of the burner blower motor rotation.
- Vibrating screen motors should be rotating in the opposite directions.
- One motor should rotate in clockwise and the other motor in anticlockwise direction.
- The Elevator side motor should rotate clockwise and the other motor anticlockwise.
- Aggregate weighing hopper and hot bin gate cylinders open to open the gates.
- Mixer paddle arms rotation from gear side should be in such a way that the right shaft is rotating clockwise and left shaft is anticlockwise.
- Check only one motor (shaft) at a time.
- Exhauster impeller when viewed from the motor side should be rotating anti-clockwise.
- Check oil level in air compressor before starting the plant.
- Remove air from the compressor at the end of each day’s operation.
- Remove water from the compressor’s tank each morning.
- Bag filters has to be heated for 20-30 mins before starting of operation daily.
- During this time run the bag filter exhausted, drum and burner blower on at very low temperature (flame).
- Before shutting down the plant run the dryer empty for 30 mins (without any material).
- During this time the burner blower, bag filter cleaning mechanism, bag filter bottom screw, exhausted should be on.
- When the plant is shut down all the components should be empty including the hot bins.
- Last batch from the mixer has to be dry batch without bitumen, without binder so that the mixer is cleaned.
- The plant will not be running to its maximum capacity for the first few days. Only after the initial few days of operation, it is advisable to increase the batch size.
If the above mentioned points are taken care, the chances of the equipment to break down in the long run will be less. The equipment can perform smoothly with desired results. We are always open to suggestions and modifications in our equipment to suit our customers to help them maximize productivity. Get More Information Contact Atlas Industries.